
The circuit chose for his first self-soldering board is actually a reflow controller. The whole thing is pretty clever, but there’s more to the story. After soldering, the now-useless heating element is converted into a ground plane for the circuit by breaking off the terminals and soldering on a couple of zero ohm resistors to short the coil to ground. The quality of the soldering seems very similar to what you’d see from a reflow oven. When connected to a bench power supply, the PCB actually heats up quickly and pretty evenly judging by the IR camera. Routing the trace around vias was a bit tricky, but in the end he managed a single trace with a resistance of about 3 ohms. Rather than a broad, continuous layer of copper, made a long, twisting trace covering the entire area of the PCB. The idea is to use one of the internal layers on a four-layer PCB, which would normally be devoted to a ground plane, as a built-in heating element. At least if you’re, who came up with a clever way to make his PCBs self-soldering. You might need to buy a commercial reflow oven - you can cobble one together from an old toaster oven, after all - but you still need something, because it’s not like a PCB is going to solder itself. Surface mount components have been a game changer for the electronics hobbyist, but doing reflow soldering right requires some way to evenly heat the board. Posted in Lifehacks, PCB Hacks Tagged 0201, 0402, footprint, footprint creation, reflow, reflow soldering Interested in learning stenciling? Get some solder paste, and read up on all the different ways you can put it onto your boards. The 04 components are in a weird spot, where soldering iron assembly is no longer really viable, but the stencil+reflow approach might not be unilaterally successful when you start off – fortunately, that’s where writeups like these come in. Are your 0402 resistors giving you grief? Perhaps, checking the footprints you’re using is a good first step. Seeing the blog post become popular, they decided to share their observations on 0201 as well, and a footprint recommendation too. Eagle CAD default footprints in particular were a problem, while a particular kind of footprint never gave them grief – and that’s the one they recommend we use. Over the years, they noticed a difference in failure rates between resistor&capacitor footprints on various boards coming in for assembly – the size and positioning of the footprint pads turned out to be quite significant in reducing failure rate, even on a tenth of millimeter scale. In an effort to get the overall failure rate down, you will find yourself tweaking seemingly insignificant parameters, and proposes that you reconsider your 04 footprints.
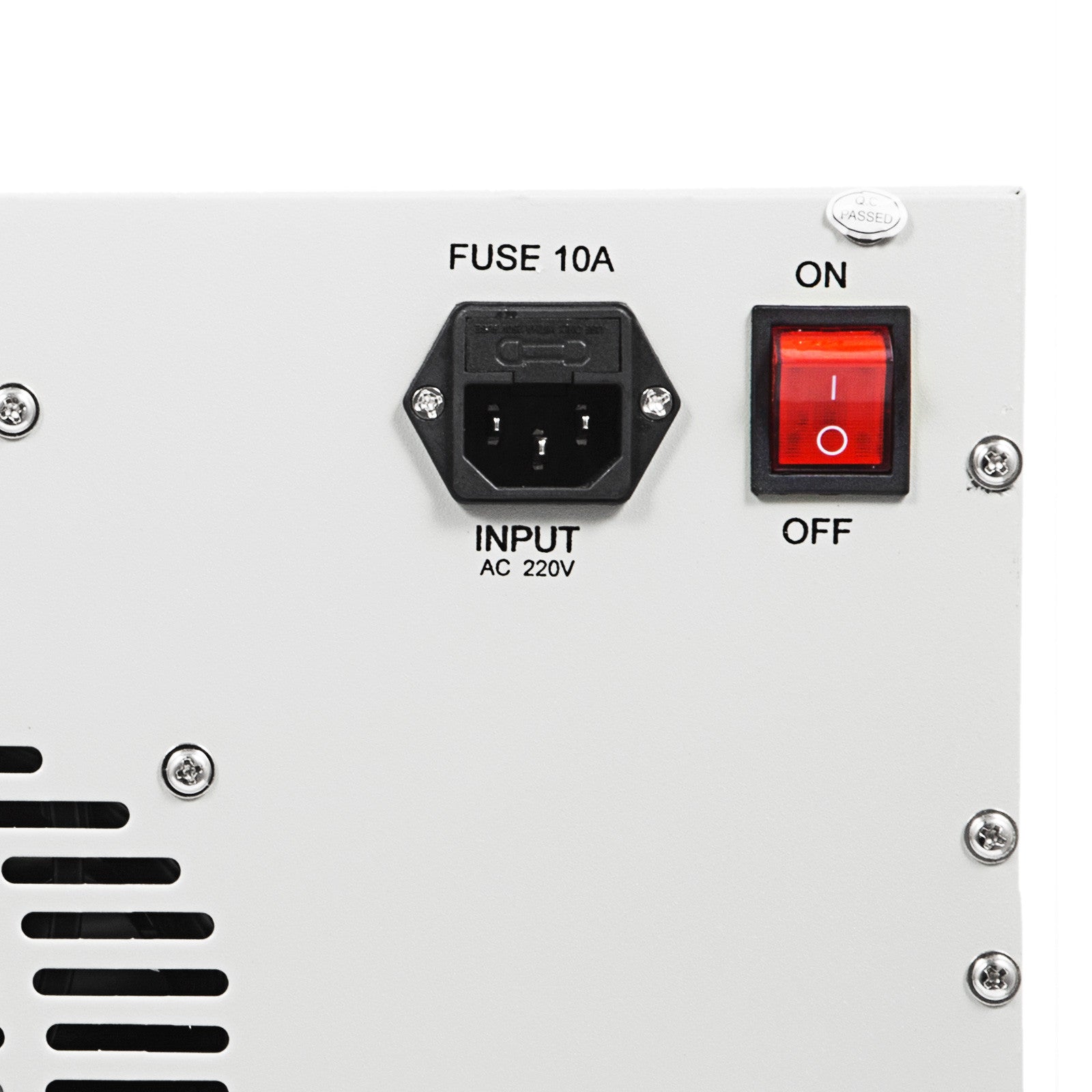

Plus, it usually goes silky smooth, the process is a joy to witness, and the PCB looks fantastic afterwards! However, sometimes components won’t magically snap into place, and each mis-aligned resistor on a freshly assembled board means extra time spent reflowing the component manually, as well as potential for silent failures later on. Assembling with a stencil is just that much more convenient – it’s a huge timesaver, and your components no longer need to be individually touched with a soldering iron for as many times as they have pads.
